This step focuses on the actual production of the switchboards. It includes the following sub-steps and manufacturing equipment:
Production Facilities
We presently own a production facility in Brampton. Furthermore, we’ve recently acquired an industrial property in London, presently in the construction phase, with expectations of it becoming fully operational by year-end. This state-of-the-art facility has been meticulously planned to serve as a strategic cornerstone in our efforts to substantially augment our production capacity. It’s a pivotal step in our commitment to satisfying the increasing demands of our clients while further elevating our manufacturing prowess.
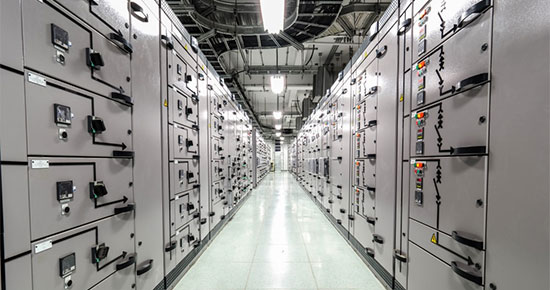
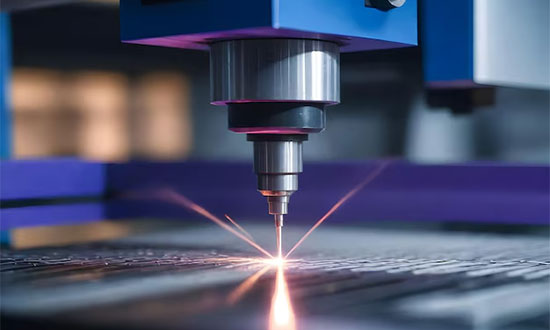
Laser Cutting Machine
We leverage the cutting-edge capabilities of our laser cutting machine to attain unparalleled precision when working with metal sheets. This advanced equipment utilizes a high-powered laser beam to intricately and flawlessly cut through the metal, ensuring the utmost precision in shaping the components of our switchboards. This state-of-the-art technology not only elevates the overall quality of our products but also empowers us to craft intricate and sophisticated designs, providing us with a distinct competitive advantage in delivering customized solutions that align precisely with our clients’ unique needs and specifications.
CNC AMADA Bending Press
We utilize our CNC bending press, a computer-controlled machine, to execute precise and repeatable bending operations with the utmost accuracy. This cutting-edge equipment guarantees consistent bending of metal sheets, resulting in switchboard components with precise dimensions and angles. The CNC bending press is an integral part of our manufacturing process, allowing us to maintain high standards of quality and efficiency in producing switchboards that meet the exacting requirements of our clients.
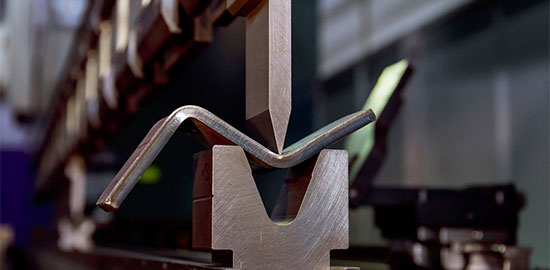
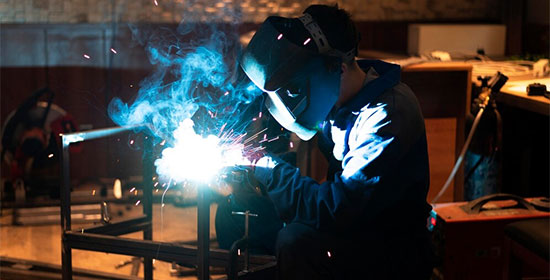
MIG/TIG/Spot Welder
Within our manufacturing process, we employ an array of welding machines, including MIG (Metal Inert Gas), TIG (Tungsten Inert Gas), and spot welders, to achieve secure component joining. These versatile welding techniques enable the creation of robust and long-lasting welds, which are pivotal in ensuring the structural integrity of our switchboards. The durability and reliability of our welded components are a testament to our commitment to delivering top-tier solutions to our valued clients.
Powder Coating Facility
Our powder coating facility plays a pivotal role in enhancing the durability and aesthetics of our switchboards. Through the electrostatic paint application process known as powder coating, we achieve a consistently even and robust coating that serves as both protection against corrosion and an enhancement to the visual appeal of our products.
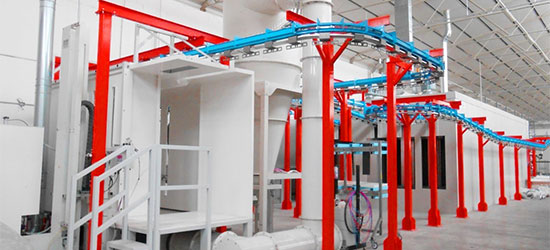
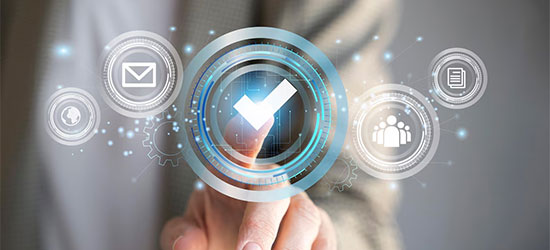
Quality Checks
Implement strict quality checks at different stages of production. This includes inspecting the materials, components, and finished switchboards to ensure that they meet the required quality standards. Quality checks help identify and rectify any defects or issues, ensuring that only high-quality products reach customers.
Testing
Conduct the necessary tests to ensure product reliability and safety. This may include electrical testing, functionality testing, and safety testing to ensure that the switchboards meet the necessary industry standards and regulations.
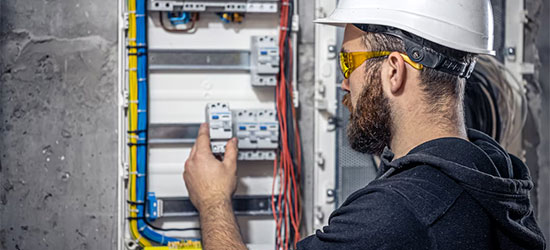
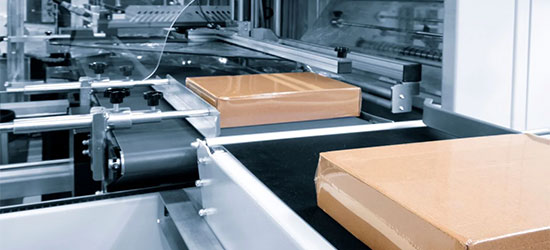
Packaging
Provide robust packaging solutions to ensure the safety of the switchboards during transportation. Secure and protective packaging minimizes the risk of damage or breakage during shipping, ensuring that the switchboards arrive at their destination in excellent condition.
By focusing on efficient product design, prototyping, material procurement, and workflow optimization, this step ensures that the final product meets the required specifications and is ready for the production stage.